REGULATORY hurdles are forcing her family’s newly-built Central Queensland meat processing facility to send cattle interstate to secure vital export sales, vertically integrated beef producer Josie Angus told a Queensland Rural Press Club lunch held in Brisbane yesterday.
Finished steers destined for the Angus family’s Signature Onfarm branded beef export clients are being sent 1000km from Clermont to Casino in NSW for processing – simply over a dispute about water.
She explained: “Our use of aqueous ozone for cleaning is a case in point. Compared to the traditional use of 82-degree heated water, it’s safer, it’s more energy and water-efficient, and it provides a better outcome and better beef. And while no single piece of our regulations or legislation demands we use 82-degree water – the simple answer that we’ve been provided with is ‘but nobody else does it this way’.”
“For us to get that US export licence is a $300,000 CSIRO study to prove a product that’s already been proven around the world for safety and efficacy.”
Ms Angus was addressing yesterday’s RPC lunch to recognise the UN International Day of Rural Women, detailing the challenges she and her family have overcome to create a $37 million processing and value-adding plant designed to handle up to 200 cattle/day.
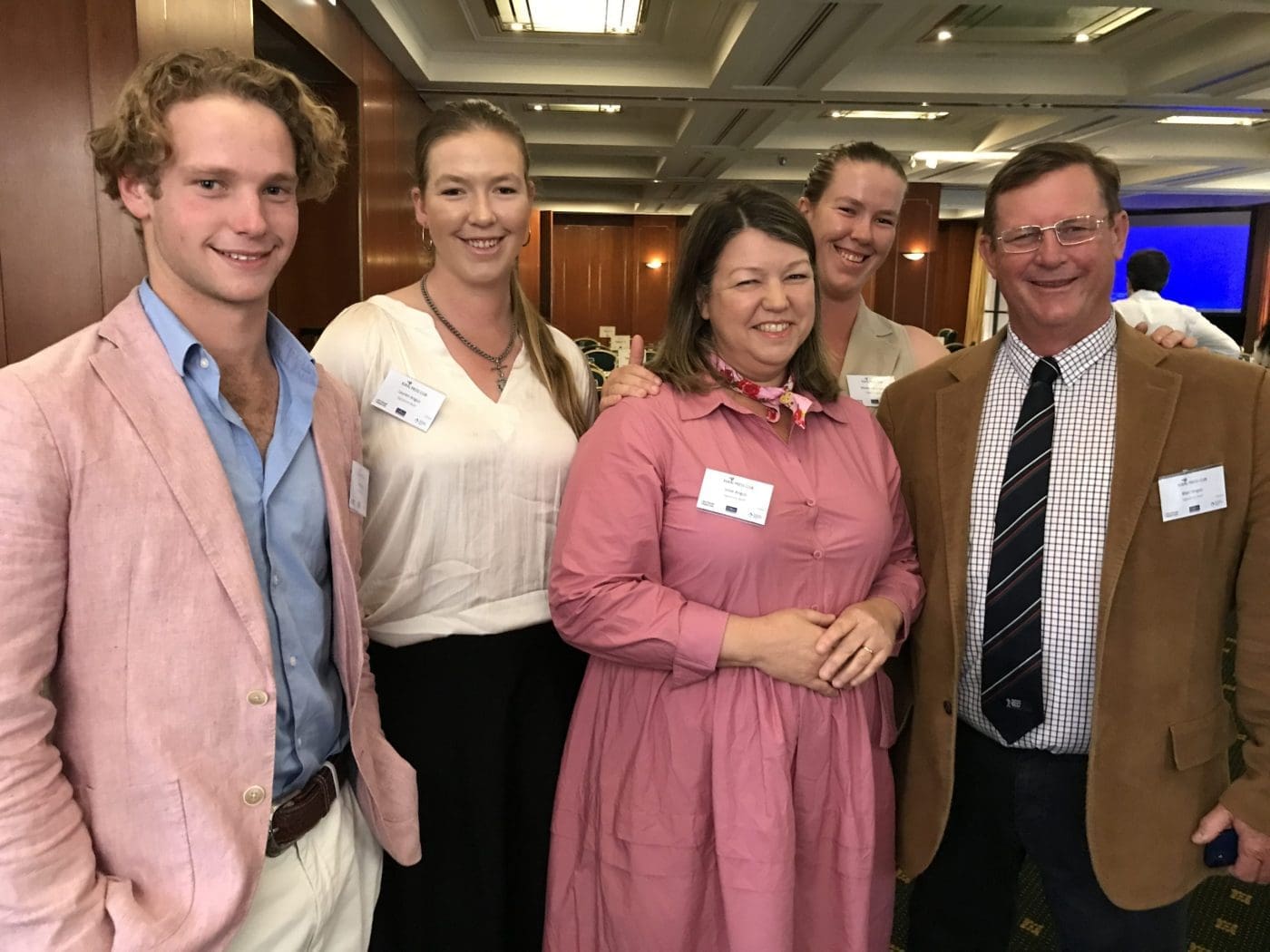
Josie Angus with her family, from left, David, Lauren, Madelaine and Blair at the RPC lunch in Brisbane yesterday.
Smaller players being unfairly penalised
She admitted writing her speech at 4am that morning. “I had intentions of getting it done earlier, but a battle with the Department of Agriculture kept me from it,” she said.
Ms Angus proudly declared the gains achieved by technology at the new plant – cutting the average Australian plant energy usage per head by two-thirds; water usage by more than two-thirds; and an Australian-first knock-box ‘that improves animal welfare out-of-sight’.
“We’ve taken the Department (of Agriculture) on a seven-year journey through building innovation, but those innovations now stand between us and exporting,” she said.
“All the way, from our council DA to our current battle for US export licencing, our country’s approach to regulation actually favours corporates over families,” Ms Angus said.
“The focus on layer-upon-layer of systems, reporting checks and check-the-checkers instead of maybe a focus on outcomes is a real and present threat to our family company.
“We are being penalised by our size. For example, our regulated microbiology testing of carcases and carton meat occurs at ten times the rate of a larger plant. The cost of our government on-plant vet works out to be 100 times per animal,” she said.
“More distressing are the barriers to innovation. The triumphant tone when a government official says, ‘It took so-and-so three years to get their US licence’ is pretty eye-opening.”
She noted that Australia sets high bar regulations. “I have no problem with that if we actually did something with it. I can’t tell you my frustration when a regulator stands there and tells me that you need to do something because the USA says so.”
Labour challenges
Labour has been another challenge for the Angus’s venture.
“The whole world seemed to run out of people to work – all at the same time. Where did they all go? In a country of 26 million, the challenge to find those people is a very simple one – you just have to be the best employer,” she said.
To run the Signature OnFarm plant at full capacity, it needs about 80 staff, but it currently employs 30.
Ms Angus admitted that the staff turnover ratio during the start-up phase “has not always met our KPI.”
Part of their approach has been to employ young local kids, to provide an alternative to the gap-year in the NT ‘or the diesel apprenticeship that will help dad fix the Toyota’.
“We also thought we’d have some pre-skilled people out of the industry who would keep the show running and provide that skilled core to teach. We probably found this the hardest part. It’s actually much easier to train than to re-train. It’s also highlighted that at a lot of the large plants, so many operators are so specialised to just one position,” she said.
“Our team are the greatest of multi-taskers. And, once again, it has been the bush kids who have really shone and it’s amazing that – when the culture is right – the skills follow really easily.”
Signature Onfarm, after just a couple of months into production took out the champion industry team at the Inter-Collegiate Meat Judging event in Rockhampton earlier this year.
The plant does not follow the traditional boning room format, with the workspace divided into teams working on individual animals, creating ‘a little healthy competition’ among staff.
Hi just read your experience with Regulates very true to the letter I had a small stock abattoir in Rockhampton 20yrs ago when the USA market was crying out for mutton & goat but like you are experiencing small fish fry quickly if my knowledge of the industry can help next time you in Brisbane ( 0401788851
Wow I just read your story. On a familiar experience I had 20yrs ago in Rockhampton with a small stock abattoir (AQIS) did exactly same to me any assistance that I can share please contact me when you come to Brisbane next time I have family in Clermont ” Terry & Charles MARKS
Well done Josie, hopefully those in high places in the meat industry take notice and support you and your team and your innovations
This article outlines a processor indulging in special pleading.
Carcases for beef are sampled every 500 for bacteriology , every 3000 carcases for small stock like sheep and goats.
This does not vary plant to plant – so why they are testing 10x more frequently is not clear.
Processors also need to understand the Dept of Agriculture does examine plant processes to get them up to acceptable standards or audit ready for the all important US or other country government audit team examinations.
This is the department assisting processors.
It is the importing countries which set the standards , not the Aust government.
How is this point not understood ?
If you are a processor wanting to export you need to pass the importing countries standards.
The Australian government has made an intergovernmental agreement with multiple countries and the difficulty for processors is that rather than each plant being subjected to endless external agency audits it has undertaken to
provide an independent verification service – thus the presence of the on plant vets.
The dominant external audit is the US audit – the Chinese, Saudis and Russians all follow similar plans with each adding extras.
The EU standards are complex but if you want to export to the EU you need to meet their standards.