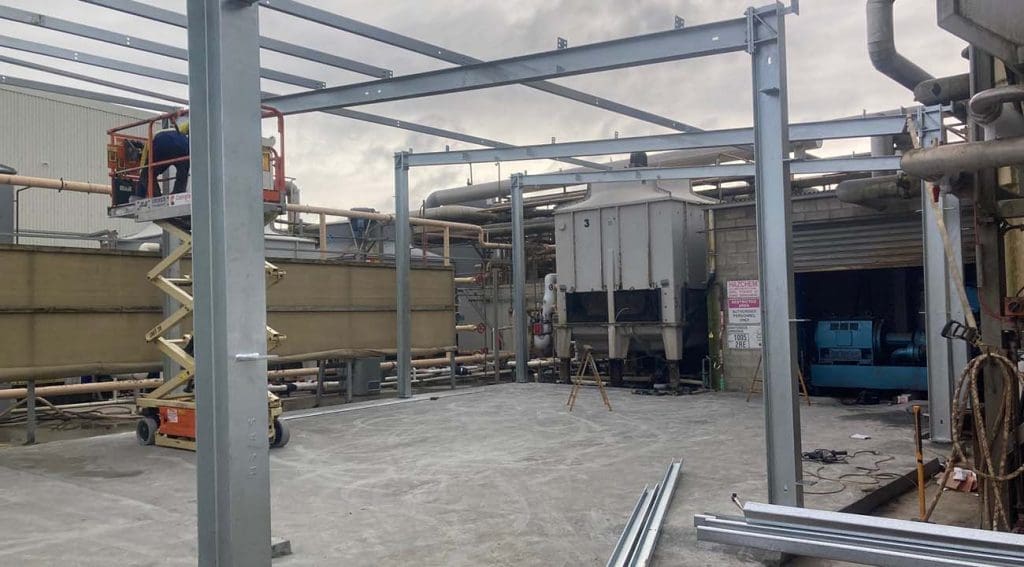
Currently under construction, the heat pump hot water system trial at Hardwicks Kyneton is expected to be operational by mid-2023.
A heat pump hot water generation trial and revamped power supply could see a Victorian meat processing company cut its annual energy and utility costs by more than $500,000.
Like all red meat processing businesses, Hardwicks uses a lot of energy.
Despite already operating a 2.5MW solar panel array and a 2MWh battery storage system, Hardwicks uses gas to fuel its hot water supply, vital for processing operations.
The geothermal heat pump upgrade will enable the site to produce enough hot water to operate at levels to improve shelf life of beef and access further export market growth, while helping to reduce the site’s reliance on natural gas by more than 75 percent.
The project will also be able to benefit from Hardwicks’ previous commitments to reducing emissions by utilising existing on-site renewable energy supply infrastructure.
The total project cost is $2.57 million with a contribution from the Federal Government’s Australian Renewable Energy Agency (ARENA) being $838,000.
Supported by ARENA, Hardwicks has embarked on a project to switch to a heat pump-driven water heating system.
Further integration of their renewable energy generation and thermal storage systems, and a new high-voltage power supply could see the company cut energy and utility costs by more than $500,000 per year.
In total, CO2 emissions from the facility are expected to fall by more than 1000 tonnes per year.
Based in Kyneton in Victoria’s Macedon Ranges, Hardwicks is now owned by Kilcoy Global Foods, employing more than 400 staff to supply food service and retail customers in Australia and overseas with beef, lamb and goatmeat in carcase and carton form.
For food safety, much of Hardwicks’ production needs to operate in a refrigerated climate below 4 degrees C. But, says Hardwick’s project manager Mark Hardwick, there is also a need for lots of hot water.
“Refrigeration is one of the key elements for food hygiene. And then the hot water is used for sterilisation of equipment, and washing down of production areas. Even things like people washing their hands, hundreds of times a day, and boots and aprons,” he said.
How not to waste waste
Refrigeration is an energy-intensive part of Hardwick’s operation, as it is for all meat processors.
Heat extracted from cold rooms, operating equipment and the production process is pumped out to escape into the environment. On hot days, the energy usage, and the energy bills, climb even higher.
In the past, the hot water side of Hardwick’s operation has relied on a gas boiler. Now, they plan to take the waste heat from the refrigerators to preheat the water.
“In a refrigeration system, there is waste heat that that is removed from the system. So we’re really tapping into that waste heat, super-compressing it for pre-heating our hot water requirements,” Mark Hardwick said.
Hardwicks’ system takes heat at around 30 to 35 degrees C from the output of its refrigeration system, using the heat pump to raise the temperature of its water supply to about 75 degrees C. That temperature boost is expected to cut Hardwick’s gas bill by 75pc.
And because the system recovers heat from the refrigeration system, it makes the cooling process more efficient, especially on hot days, and cuts refrigeration water use as well.
Hardwicks will still use its existing gas boiler, much like an instant gas boiler at home, to top up the water temperature on demand. But savings are still expected to top $280,000.
Mark Hardwick said if the trial was successful, the company may drop gas altogether.
ARENA is also supporting a switch in Hardwicks’ electricity supply from low-voltage to high-voltage. That is projected to realise a network tariff reduction of more than $235,000.
Heat pump hot water system overcoming barriers
The Hardwick’s project kicked off in February. When operating in mid-2023 it aims, among other things, to provide an improved understanding of how to reduce the perceived risks of retrofitting heat pumps for industrial process heating.
Mark Hardwick acknowledged the choice to substitute their existing gas system was, initially, not an easy one.
“Hot water generation through natural gas is well-proven, it’s quite cheap,” he said.
“When the heat pump was put across our desk…we did the first feasibility study and said if we can make it work this is a really good project,” he said.
Australian Renewable Energy Agency chief executive Darren Miller said the demonstration project is intended to boost industry uptake.
“The project offers us the opportunity to trial how using heat pumps can reduce reliance on natural gas and prove to the industry that this is technically and economically feasible and a viable solution to dramatically reduce emissions at their facilities,” he said.
“Hardwicks is at the forefront of helping to reduce emissions in the meat processing industry. “Having already installed on-site solar PV and battery, it is now able to demonstrate how the hot water demand of industrial processing can be managed with the addition of heat pumps and use of thermal energy.
“This is a solution that we could see being replicated across other businesses in the industry,” Mr Miller said.
How do heat pumps work?
A heat pump works like a refrigerator in reverse. Instead of extracting heat from a targeted space – say the inside of a kitchen fridge and its contents – and then dispersing it, the heat pump effectively captures that heat energy, concentrates it and moves it to where it is useful.
Imagine if your kitchen fridge was made to work in reverse – you would end up with a slightly cooler kitchen and a sort of lowish temperature oven inside the fridge cabinet. Put a kettle of water in there and you would get warm water. Turn it up to 11 and you might even get hot water.
Industrial heat pumps do this on a gigantic scale. A kitchen fridge might have a power rating of around 150 watts. The 1MW thermal capacity heat pump that Hardwick’s is installing operates off a 250kW electrical power supply – equivalent to 1500 fridges running in reverse.
To get an idea of the decarbonisation potential of heat pumps, recent modelling by the Australian Alliance for Energy Productivity (A2EP) indicates a reduction of 10 million tonnes of CO2 per annum is possible by 2030 by using all forms of heat pumps across all industries.
I first learnt about geothermal heat pumps while at University in 1983 and the technology was not new then – it will be great to see it used more often now that its environmental benefits are finally being recognised.