WHILE some large red meat processors see DEXA scanning technology’s financial payback as being contingent on the application of robotics and automation, one NSW lamb processor is approaching adoption of DEXA scanning solely for performance feedback and plant efficiency purposes.
Gundagai Meat Processors provides a service kill for a number of large lamb supply chain clients including Coles, processing 4000 lamb a day, amounting to around one million lambs each year.
GMP’s chief executive Will Barton gave an outline of the company’s progress and future plans with DEXA to an audience of 150 young undergraduates attending the 2019 ICMJ Wagga gathering earlier this month.
Mr Barton said his company saw its transition into DEXA as being a part of a process of better servicing its fee-for-service lamb slaughter customers through the provision of feedback and technology.
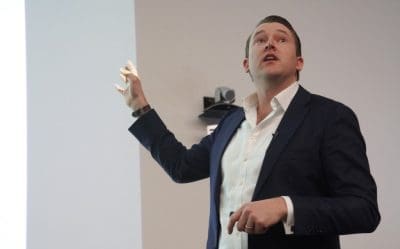
GMP’s Will Barton
“We think we, as processors, have a really important role to play between the producer and the consumer, and we’re trying to take that role a little more seriously in what we are about to adopt through DEXA, than what we have in the past,” he said. “We’re starting to think about these things differently, and perhaps not focussing as much on what people have been focusing on for many years.”
“We have this unique position, as a processor, converting live animals from a producer into an end-product for a consumer, and we also have this critical role in feeding the information back down the chain. We’re not quite there yet, but we’re getting closer to a positon where we will be able to respond to the market according to the information we gather in the plant.”
Changes in feedback information
Mr Barton said as it had for the past 50 years, the lamb industry currently relied on carcase weight and fat score, using palpation of live animals, which was “horribly subjective and wildly inaccurate.”
“It’s why we don’t have more product differentiation in lamb, because even if you did have a special product, we wouldn’t be able to stand by that, as a processor, and explain that the product was real and right, without evidence to prove it.”
Gundagai has now completed installation of its DEXA X-ray unit at the end of its slaughter floor, and while it carcase scanning is already taking place, the system is not yet fully commissioned and calibrated.
“We are continuing to collect weight, and for the timebeing will continue to collect fat score, but over time we will move to DEXA to objectively gather information about fat score,” he told the ICMJ audience.
“DEXA will give us lean meat yield, bone percentage and fat percentage for each carcase, and we have also started collecting individual animal defect and disease data based on offal condition, building a much more comprehensive set of feedback data for suppliers,” Mr Barton said.
“We’ve come an incredibly long way in a very short period of time, to be in the position that by the end of the year, every animal that is processed at GMP will be able to be associated with feedback than includes yield and fatness, and what animal health issues the animal may have had during its life, on a carcase-by-carcase basis.”
Challenge in balancing yield with meat quality
The challenge surrounding the provision of yield information was in ensuring that producers did not over-react. “If we set price signals on meat yield to producers, then we run the risk of turning the lamb category into a ‘chicken or a pork’, which is essentially something lacking in flavour and bred for yield, which must be accompanied by a sauce to be eaten. That’s not where we want to go,” he told the ICMJ students.
“Instead, the lamb industry now needs – in a screaming hurry – an objective eating quality measure, and the industry is obviously working on that as we speak. We will start trialling a measure at Gundagai, based on intra-muscular fat, in the next three months,” he said.
“Once we get those things in place, we are working on providing lamb suppliers and our service kill customers supportive feedback on yield, eating quality and animal health performance. It’s about developing the old weight/fatness based feedback sheet into something that has a high level of transparency, giving insights into all these other things that we are gathering information on.”
GMP plans to give producer education a high priority, running sessions so stakeholders better understand what the data means in terms of maximising profits, improving animal health performance and ‘what it is that the consumer is after’ in lamb.
As an extension of that, GMP also plans to introduce a supplier benchmarking analysis – a process which was ‘really devoid’ in the industry at present, Mr Barton said – comparing each producer’s individual data with the broader group, in terms of weight, yield, days to market, animal health performance and other traits.
“We’re really excited about the potential to do it better,” he said
Turning discussion towards the implications in the DEXA adoption for the plant itself, Mr Barton said to date, lamb processors had been very good at using the whole of the carcase and its by-products.
“The price of livestock and the economics around processing lamb have meant that we’ve had to be really good at making sure we use everything effectively. We’ve conquered waste – we don’t slaughter something and then not make full use of the material. We’re in the position where we are now collecting bile from gall bladders, for example, for Chinese medicine, at a rate of 70ml per lamb.”
‘Data-rich’ environment
“But what we’re not doing as well, which are about to embark on under DEXA, is using the carcase to its highest and best use. We’re at this stage now where we are gathering all this information about the carcase so we can find the best market it needs to go to, and make sure we sell it correctly.”
“In the past we had weight and fat score on lamb. Now we have this data-rich environment, in which we are collecting a range of other information and our goal needs to be to find the optimal market for every cut inside every carcase, using really advanced carcase sortation systems.”
“Part of this optimisation journey is about making sure we are boning efficiently. We know that very fat carcases are difficult to bone, from a labour viewpoint, to minimise waste to make sure we don’t direct a product with a high level of fat into a market that is going to be sold as a denuded product, but to keep as much of that fat with the carcase, based on what the end consumer will pay for, to maximise profit of cuts in each market.
In concert with its shift into greater carcase assessment and segmentation of carcases, Gundagai has just completed a major upgrade of its carcase chillers. Previously, based on the old simple parameters of carcase weight and fatness, the plant had chiller capacity for 3600 lambs, with carcases divided simply into heavier and lighter bodies, either side of 23kg.
The chiller redesign now sees two chillers dedicated to temperature reduction, with all carcases passing through the same first-stage chilling process, requiring six hours. Three additional chillers are now used for sortation, based on carcase data collected through DEXA and other means, increasing total capacity to 4750 bodies.
A sortation decision is made using RFIDs embedded in rail hooks, directing different carcases to various rails for boning for different market end-pointsi, after DEXA scanning.
“Because we now have no-touch carcase transfer through this whole process, our workplace health and safety issues are minimised, by not having a team of people using their shoulders to push carcases around. Microbial loading has been reduced significantly because personnel are not touching carcases, and our cleaning costs have been reduced,” Mr Barton said.
“It’s been quite an interesting exercise in making sure our plant is capable of matching the needs of greater data collection, and playing this role between producer and consumer in an effective way.”
Different approach
Mr Barton said most livestock industry stakeholders when they thought about the DEXA technology thought about driving automation, to deliver precise instructions about cutting lines for robots.
“But our approach has been different. For us, it’s not about automation, at this stage. There is a mutual benefit to be gained by the processor by enhancing feedback using DEXA in this way. It’s not as if we have to forego profit or efficiency to be able to generate something for a producer, but it just requires a different thought process.”
Increasing consumer expectations
Mr Barton said with rising prices for lamb due to a range of reasons, consumer expectations about the product were steadily increasing.
“The consumer who enjoys lamb will pay for it, but they’re going to have an expectation around quality, biosecurity, traceability and all number of raising claims – and we need to be able to prove that. It’s no good doing all of this work and then telling the customer, ‘Our product is better – trust me’ – unless every time we slaughter an animal we can prove that it is better, and we can tell the market the quality is there, and it has been checked and verified.”
“There’s no doubt that the global market outlook for lamb remains bright, but we can’t continue to expect to dish up ‘commodity’ product and expect those prices will remain strong.
“As we catch up with the consumer, who is requiring more information about the quality of the product and where it comes from, success in the supply chain is dependent on us, as processors, playing our part in that role between producer and consumer.”
“For us at Gundagai, that means provision of meaningful feedback to farmers, improved and optimised use of the raw material, carcase optimisation, and being responsive to those consumer needs and making sure those signals are fed back to the producer.”
Automation on the horizon?
During questiontime, Mr Barton was asked what the next step was in the project, and whether automation was on the horizon.
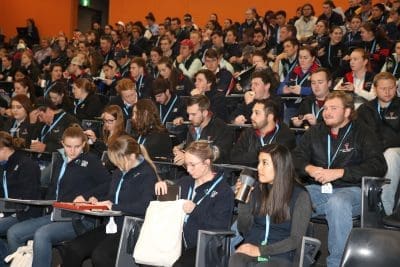
Undergraduates involved in the ICMJ conference in Wagga recently
“We’re on this journey to get the feedback as good as we can. So when competing processor buyers come into the Gundagai region to pilfer our lambs, the producer is going to say, no, I’m sending to Gundagai, because I know the value I get from the feedback. The next step is to make sure that those producers are getting absolutely market-leading intelligence on what they are doing, which is meaningful and helps them to be profitable. That includes an eating quality measure, because that is the missing ingredient in what lamb has at the moment.”
He said the obvious next step, within the GMP business, was in also using the DEXA outcomes to drive automation and robotics.
“Currently, it’s a scale issue for us. We’ve been described as the ‘biggest little lamb plant’ and the ‘smallest big lamb plant’, but we are currently still too small for a lot of the fancy automation and automated cutting technology associated with DEXA.”
“We’d need to grow volume to get there. One way we believe that can happen is in providing that feedback focus to farmers, and assisting our existing service kill clients to develop a premium line, based on the feedback we collect.”
A second question asked about potential labour savings at the plant through DEXA.
“For any processor adopting DEXA, the low-hanging fruit is to automate to get rid of repetitious and lower-skilled tasks. We don’t see any likelihood that our level of employment will go down, as a result of DEXA, but automation and sortation technology will instead help us to scale-up production.
“But with technology like this, work skills change. We now have four full-time electricians who have learned PLC coding and more advanced skills to keep our new carcase chiller sortation system rolling.”
“When I look back at my childhood it was about how many wheelbarrows and shovels we have, and how many people we need to operate them. Today it is very different, and there are opportunities in all sorts of fields. The skills required are increasing and changing, and new requirements are popping up all the time.”