Digital technology is helping some of Australia’s largest beef industry players to deliver cattle and beef exactly to their customers needs, as MLA’s red meat digital forum in Brisbane heard last Thursday.
EVERY night, a muster with a difference occurs across the Australian Agricultural Co’s vast cattle stations.
It doesn’t involve physical stockmen or women, but plays an equally vital role in helping the enormous cattle and beef supply chain to give its customers exactly what they want.
Every night at midnight, data from AA Co’s 500,000 cattle on 22 properties is synchronised into the company’s digital database.
There it is joined by more data electronically-mustered earlier each day from the 40,000 cattle in AA Co’s feedlots; from four processing plants, including its own Darwin abattoir, and from its sales and customer divisions.
The mass intake of data is then accessed by various software programs to produce information in a form that supports AA Co’s daily decision-making and forward planning.
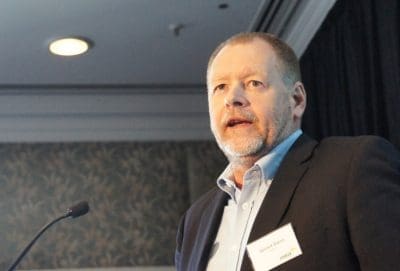
AA Co’s Gerard Davis
AA Co General Manager of Innovation and Strategic Development, Dr Gerard Davis, provided examples of how the data is used at MLA’s digital strategy forum in Brisbane last week.
Data fed into the company’s supply chain modeling software provides continual updates on 3,000 movements of AA Co cattle across the country, out to two years in advance.
“This model enables us to look two years in advance and be able to say the cattle that are due to be processed on this week in 2018 are in the supply chain and they will actually arrive,” Dr Davis explained.
“What our customers are looking for is that we have that predictability in being able to deliver.”
Dr Davis said digital technology was vital in helping AA Co to run a demand-driven, consumer-responsive integrated supply chain.
(Believe it or not, what AA Co is doing in this space does not fit the true definition of “big data’, which refers to data sets so large, mass processing power well-beyond the capacity of normal desktop computers is required to manage it. As Dr Davis explained to the forum: “The real definition given by the director of the Big Data Centre at QUT here in Brisbane is that big data is ‘inconveniently large’.)
Could the best cattle today be the average in five years time?
Teys Australia believes this is possible, as the beef supply chain harnesses data technology and a customer-focus to create price signals that reward production of cattle that meet specific customer requirements.
Every dollar that flows into the beef supply chain originates with the customer.
“The consumer always has to be front of mind,” Teys’ general manager corporate services Tom Maguire told last week’s MLA digital red meat strategy forum.
“The only dollars we all enjoy come from them. We are absolutely convinced there is value if we get it right for those people, and if we get it right all the time.”
However, giving a customer what they want creates a unique challenge for meat processors, because they are not involved in the production of the end product from the very beginning.
“We disassemble things,” Mr said.
“That puts unique responsibility on us, because if we want to give that end consumer exactly what they want, then we have to send the right signal back to the producer.
“We have got no hope if we don’t get that right, because all we are doing is pulling it apart and selling the pieces.”
Objective processing data shows that, despite subjective visual assessment that might suggest the cattle in a typical mob are all but identical, wide-variation exists within mobs and across mobs of cattle.
A Teys slide showing the processing performance of six mobs recently processed at Biloela highlighted a difference between the best and worst of $1500 per head.
Teys believes that providing better data back to producers can reduce this level of variation.
Under the current grid system, producers are paid the average.
Data should show producers the true value of each animal, how to identify the good and bad, and the reasons for that value difference, so producers can make decisions, Mr Maguire said.
Price signals linked to yield and quality parameters would then reward improvements.
The current issue is not a lack of data.
For example, a supplier of 180 cattle to Teys would typically receive 21 pages of information at the moment, with separate reports covering kill data, chiller assessment feedback, specific MSA feedback, results against the grid and more.
Mr Maguire said simple information was needed to enable producers to make smart and quick decisions.
“We have to get that information right,” he said.
“Very simply, we need to give information back to our suppliers, in a useable form, so the very best today can become the average in the future.”
In many ways the industry was already getting data right.
The feedlot industry was well advanced on this journey.
Teys has databases into which vets routinely report animal health data from its feedlots.
MSA quality data from the same cattle after processing goes into the same database.
That enables Teys to benchmark mortality and disease prevalence across its feedlots and plants against the national average. It can also do the same for meat quality traits.
“These are the kind of simple pictures we have to build for the whole industry,” Mr Maguire said
Teys believes a lot of poor carcase grading performance can be traced back to animal health. Animals with compromised health during their lives did not develop the same way as healthy animals.
A powerful example of how this information can be used to benefit the entire supply chain has been proven in Northern Ireland.
In what has been a ‘game changing’ move, meat processors there send animal health data back to producers.
This has dramatically reduced liver and lung diseases in the Irish cattle herd.
Teys plans to implement a similar system here in March next year.
“The next phase to get animal health data is a really important one, it is about getting animal health feedback back to our supply chain,” Mr Maguire said.
“This has been a real failure of the industry for 40 years, because this has been collected every day in every meat plant by Commonwealth government inspectors, but they don’t record the data.
“With the advent of third-party meat inspection, we can get them to do that now, and produce feedback to producers.”
The implementation of objective measurement will also help plants to evaluate how much saleable product there is.
There is still work to be done, however.
“We have to get the data standards right,” Mr Maguire said.
“It is no good Teys having one objective carcase measurement machine, JBS buying a different bit of technology, and producers having no hope of comparing apples with apples.
“So we need to get the data standards right, the technology providers can follow.
“The important thing is to get the data in a form that can be actioned and decisions can be made.
“I absolutely believe the best of today can be the average in 5-7 years if we can get it right.”