A NATIONAL fund of at least $1 billion is needed to improve the standard of Australia’s distressed rural roads, livestock transporters have told a Federal committee developing a roadmap for Australia’s future transport needs.
The Federal Government has committed to developing a new national freight network and supply chain strategy for Australia.
A final report is currently being prepared following a round of public submissions, and is expected to be handed down this month.
Livestock transport and red meat industry groups were among the 120 organisations and individuals to provide written submissions to the inquiry committee.
Priorities called for by rural industry groups included:
- A $1 billion national road fund (ALRTA);
- Expanding the network of sealed roads in Northern Australia (NTCA);
- Funding support for a network of roadside effluent disposal facilities, and rules compelling livestock producers to appropriately prepare animals prior to road transport (ALRTA);
- Opening network access to A-Doubles (RMAC);
- Reinstating the Auslink Strategic Regional Program (RMAC);
More details:
$1 billion national road fund: In its submission the Australian Livestock and Rural Transporters Association (ALRTA) urged the Australian Government to establish a national fund of at least $ 1 billion to improve the standard of key rural freight and tourism roads.
Australian agriculture had ‘tantalizing opportunities’ on its doorstep in Asia, but could not capitalise on those opportunities without the ability efficiently deliver agricultural commodities from farms and processors to international markets, the ALRTA wrote.
Over two-thirds of Australian agricultural production is exported.
However, Australian agriculture is three times more reliant on land transport than its international competitors. With New Zealand, Australia has the highest total transport cost for exports across all countries in the OECD.
Fuelling inefficiency, the ALRTA says heavy vehicle operators had been overcharged by more than $200m a year since the 2014 PAYG tax review.
Chronic under investment by Governments had left many roads servicing Australia’s agricultural production zones without a significant upgrade for 70 years or more.
Only 25 percent of revenue from the fuel tax is spent on road infrastructure and maintenance.
Many of the rural roads upon which the nation’s export economy depends were now in “serious distress”.
“To the point that local authorities are threatening to reduce road access or impose speed restrictions at the very time when we should be doing quite the opposite,” the ALRTA wrote.
The ALRTA said it acknowledged and welcomed the various pools of money Federal and State Governments had allocated to assist in improving rural and regional roads. However, in reality these programs were just scratching the surface, and were band-aid solutions for a problem of major national significance.
“Australia cannot afford to wait another decade or more for current land transport charging and investment reform these reforms to be agreed, implemented and long-term infrastructure plans developed,” the ALRTA said.
“If Australia does not act now to lift the standard of our country roads, a significant part of the ‘windfall gain’ arising from burgeoning trade with Asia will never reach the farm gate.”
Action needed to manage effluent issue: The ALRTA said it also wants the Government to establish a network of roadside effluent disposal facilities on key freight routes, and Government and to compel livestock producers to appropriately prepare animals prior to road transport.
It says livestock effluent is a known vector of Foot and Mouth Disease, but little is being done to provide a decent network of truckwashes and managed effluent disposal sites. Major meat processors based in highly populated areas of Australia faced significant future risks to their business because of local concerns about effluent impacting public amenity.
“In New Zealand, National and Regional Governments are jointly funding, building and operating purpose-built livestock effluent disposal facilities on public roads.
“This is exactly what is needed in Australia for the livestock supply chain to co-exist and grow alongside an expanding urban population.”
A basic site will cost around $250,000 to construct, with annual maintenance costs of $30,000 thereafter.
The ALRTA said this cost must become part of the statutory service level standard applied to key livestock freight routes in Australia. “All costs associated with the construction and maintenance of such facilities could then be factored into the cost base for calculating heavy vehicle charges and recovered from industry.”
“This approach will provide a sustainable funding base and enable road managers to routinely consider the need for strategically placed roadside effluent disposal sites when making road investment decisions over the longer term.”
Reduce restrictions on High Productivity Vehicles: The ALRTA said there were two obvious ways to drive down transport costs for the Australian cattle industry:
- Use more productive vehicles such as b-doubles, b-triples and road trains; and
- Use the most direct route from the point of production to the point of sale, processing or export.
In Australia, high productivity vehicles (HPV) are also known as ‘restricted access vehicles’ (RAV), the ALRTA noted.
“It is often the case that a HPV can operate for part of an intended journey, but is not legally allowed to operate on the ‘first mile’ or ‘last mile’ of a transport task.
“As a result, either a less productive vehicle must be used or the operator must apply for a permit to access otherwise prohibited parts of the network.
“Decisions about HPV access should be based on engineering principles, network design and measurable impacts – not underlying attitudes towards industry or heavy transport or a desire to raise revenue at the local level.”
Transport costs biggest expense of pastoral enterprises: The Northern Territory Cattlemens’ Association pointed out that over 1.6 million cattle were transported by road in the NT in 2016.
The average distance to port or slaughter for an NT cattle station is 1135km.
Of the 22,000km of roads in the NT, more than15,000km – or 70 percent – are unsealed.
The cost of transport for heavy vehicles on unsealed roads in the NT is 30 percent higher than on sealed roads, according to the Northern Territory Road Transport Association (NTRTA) figures.
Many transport operators, in addition to their standard cartage fees, add a further charge of $0.10/deck/km (and as high as $1.80/deck/km on some very poor roads) for working on unsealed roads.
Added to this is the cost of stress and bruising to livestock caused by rough roads, which results in significant price penalties at market.
CSIRO figures show that transport costs in the northern cattle industry can be as high as 40 percent of the total sale price of an animal.
Even roads that are sealed were typically sealed back in the 1970’s and 80’s. The specifications of that time were designed to handle a much smaller freight task than they carry today – the weight of trucks and trailers has increased dramatically, as has the volume of heavy traffic as the beef and resources industries have expanded.
As a result the road network, both sealed and unsealed, is deteriorating rapidly.
‘on one corner of the Buntine Highway, four road trains have overturned in the space of one year’
Not only does this create inefficiency, but also a dangerous environment to drivers and stock alike: “For example, on one corner of the Buntine Highway, four road trains have overturned in the space of one year, resulting in the deaths of many livestock on board and a serious danger to the drivers,” the NTCA wrote.
The NTCA called for a dedicated, targeted, strategic and long-term annual funding program, which identified key beef roads, upgraded those roads to provide all-weather, year-round access to market, and improving the sealed network to handle the present-day and future freight task.
Reinstatement of Auslink Strategic Regional Program: In its submission the Red Meat Advisory Council highlighted modeling showing improvements in road infrastructure could generate an additional $700 million in revenue and employment of a further 4000 people in the next decade.
RMAC said the former Auslink Strategic Regional Program was successful in solving smaller scale supply chain problems that crossed local Government boundaries in regional areas, and a worthwhile template that should be reinstated.
Next major opportunity – the A Double: Historically, the development of double and triple road train combinations was a major productivity enhancer for Australian livestock and meat transport. In the late 1980s, Australia adopted the B-double, which provided superior braking and tracking capability and freight volume gains of up to 50pc.
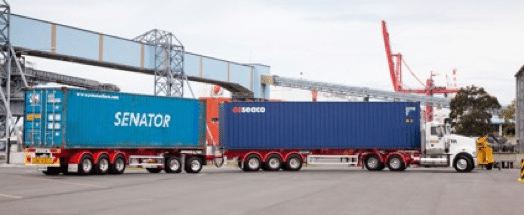
Next major opportunity? The A-Double can carry up to two 40-foot shipping containers at or near sailing weight.
The A-Double is two articulated trailer units with an innovative steerable converter dolly arrangement which allows more payload to be carried, without creating adverse road wear outcomes, or performing in a more unstable way than an articulated truck or B-double on the road. Austroads research suggests that Performance-Based Standards-accredited vehicles such as the A-Double offer safety levels between 60 and 70 per cent higher than the existing general fleet.
RMAC points out that many meat processing plants are restricted to using the 20-foot shipping containers at a time when being able to carry two 40-foot shipping containers would deliver vital supply chain productivity gains for the sector.
Opening network access to A-doubles would deliver open nominal freight volume gains of 100 per cent compare to B-doubles.
In a case study in its submission, RMAC said the ability to use A Doubles over B Doubles would generate Singleton export accredited beef processing plant EC Throsby an annual truck operating cost saving of $994,000, plus a further saving of $497,000 in annual container rental costs.