What if protein was no longer a limiting factor in our northern beef systems? Qld beef industry RD&E professional Dr Lindsey Perry looks at how small-scale, on-farm ‘green’ ammonia technologies could provide localised systems to potentially fill the protein gap in future.
RECENT articles have highlighted the technological advancements in converting atmospheric inert nitrogen gas (N2) into available nitrogen compounds for use as fertilisers.
Industrial ammonia production underpinned the agricultural “Green Revolution” of the mid-1900s, tripling cereal crop yields with a 30 percent increase in land use and lifting millions out of poverty.
Ammonia-derived fertilisers drive modern agricultural production. Urea, ammonium nitrate and nitric acid, respectively comprise 55 percent, 26 percent and 13 percent of the world’s synthetic nitrogen fertilisers.
Industrial ammonia production is also one of the world’s largest CO2 emitting chemical processes.
Traditional Haber Bosch requires intensive energy through a feedstock of natural gas or coal. High fossil fuel inputs skyrocket the GHG emissions profile of ammonia fertilisers, estimated at ~2 percent of total global emissions.
Additionally, transport by road and sea of fertilisers from large, centralised Haber Bosch plants leaves Australian producers vulnerable to price volatility and supply disruption.
The race to reduce emissions by replacing natural gas and coal with renewable energy (the ‘green’ in green ammonia) has incentivised rapid expansion of R&D in this space over the last decade.
Perdaman’s $6 Billion urea plant in the Pilbara is likely to support the majority of domestic fertiliser needs in the next few years.
Grain Central and AgCarbon Central ran an excellent article noting the rise in smaller units including localised on-farm options to produce ammonia and derivative N fertilisers.
Most of the technology is at the research and venture capital stage although a few on-farm pilot trials are beginning.
The grains industry has been quick to realise the potential of green ammonia due to the scale of fertiliser use in the sector, price volatility of imports and the high emissions profile associated with fossil fuel reliant industrial fertiliser production.
Are we overlooking the opportunity for the livestock sector?
In Australia’s northern beef production systems, and many others around the world, protein is the first limiting nutrient.
Nitrogen (N) is the essential component of protein.
As pasture quality declines, low protein content of the diet limits growth and reproductive efficiency of livestock.
Filling this feed gap with a true protein is often uneconomic depending on commodity prices.
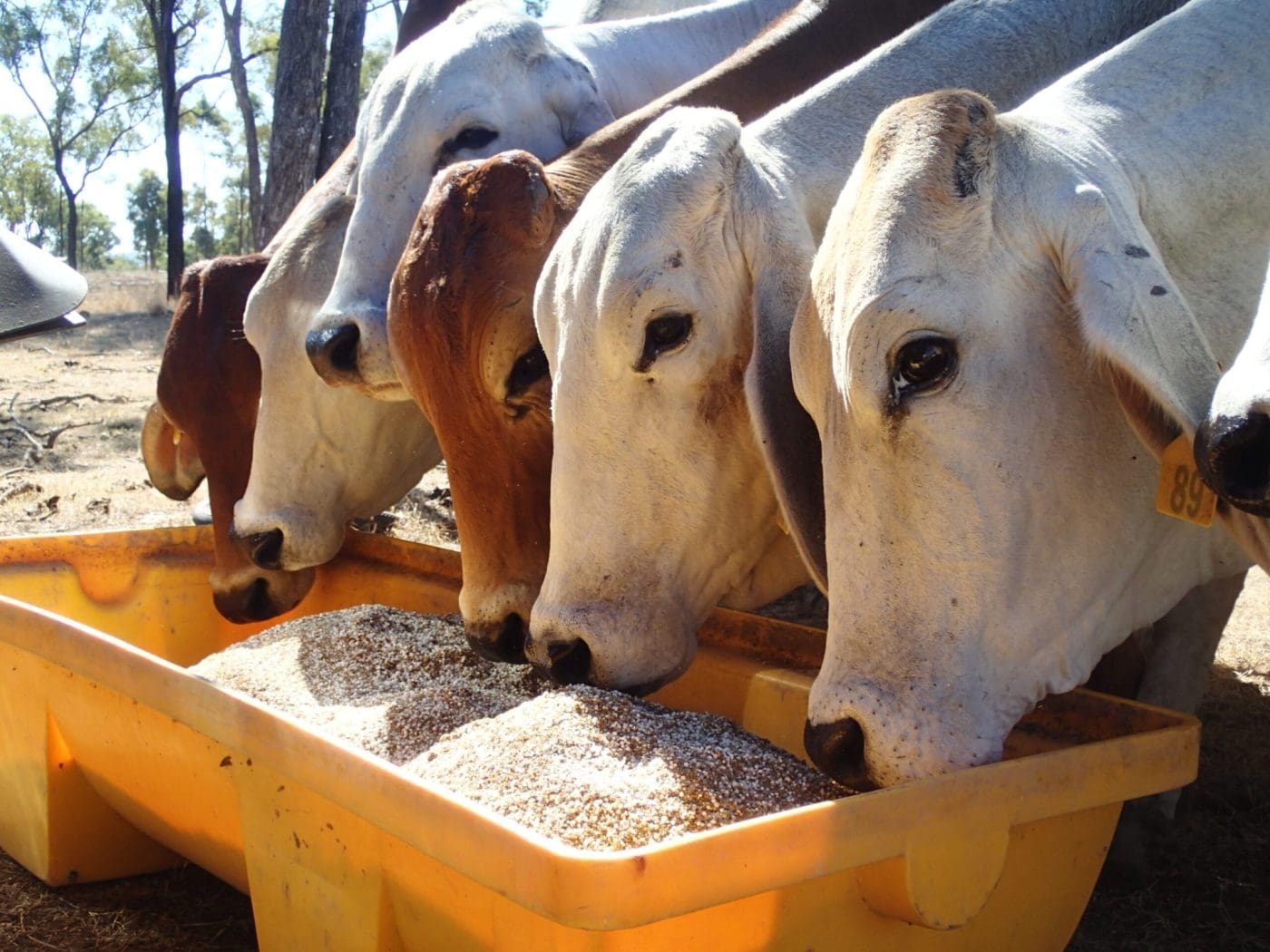
Picture: FutureBeef. Stockfeed suppliers estimate around 10,000-15,000 tonnes of urea is used annually in the northern beef industry.
Supplementing livestock with a non-protein nitrogen (NPN) source like urea through the dry season is common.
Although quantities are not tracked stockfeed suppliers estimate approximately 10,000 – 15,000 tonnes of urea is used annually in the northern beef industry.
Supplement is one of the largest costs for an extensive beef operation totalling $40-$100 per breeding cow per year in extensive northern beef regions. In the context of large operations with tens of thousands of cattle, these figures quickly add up.
Supplementing livestock with NPN does not solve the true protein deficit of dry season tropical pastures. It provides an N source for rumen microbes to convert into ‘true’ protein and supports microbial population growth. An active, growing microbial population improves feed utilisation and increases feed intake (20-30 percent for urea). In this way, NPN supplementation minimises weight loss over the dry season when pasture quality is low. Microbial cells absorbed in the small intestine provide additional protein for the animal. Microbial protein supply provides 80-100percent of the true protein utilised by cattle grazing low quality tropical pastures. The use of NPN sources have for decades provided a cheaper, accessible option to support microbial protein synthesis. Queensland Department of Primary Industries recommends rates of 60g urea per day for a breeding cow and 30g for a growing animal once pasture quality has declined.
Emerging technologies
Emerging small scale ‘green’ ammonia technologies provide potential for the livestock sector to fill the protein gap for target stock classes (e.g. heifers, growing steers).
This could look as simple as producing N fertiliser to grow crops in a diversified area on a pastoral lease (pivot or an area of dryland crop production) or convert the N produced into an alternative protein.
Prof. Dennis Poppi highlights a body of work in algae production as one option to convert ammonia or other NPN produced by these units into a true protein source safe for livestock. Among these, spirulina is gaining interest overseas as an animal feed constituent that can be cultivated free of arable land, in bioreactors or open ponds and has a crude protein content of >60 percent dry matter. Algal production systems at scale are not without their complications and come at a cost.
However, if cheap protein options can be locally generated where they are needed, is there scope to improve cattle growth rates and access higher value markets in the more marginal of our northern production systems?
Small scale NPN production opportunities
In the USA, traditional Haber Bosch processes adapted to use renewable energy and electrolysis are at the prototype stage. FuelPositive put one of the first farmer owned pilot units on farm in Manitoba in June 2024 but it is yet to be fully operational (see more here – Green ammonia moves to reality on Manitoba farm). The unit runs off the hydro-electric grid, uses electrolysis of water and nitrogen from air to produce 100 T anhydrous ammonia per year, 20-25 percent of the 11,000-acre grain operation’s needs. Proton Ventures (NFUEL units) have plug and play skids and do not need site preparation. These units have the capacity to recycle waste from landfills or anaerobic digesters. The unit can produce 3 MT of ammonia per day. Similarly, the IAMM Unit from AMMPOWER creates high purity anhydrous ammonia from electricity, water and air. These units produce 4 MT of ammonia per day and can be stacked to scale up production to save on transportation and logistics costs. The latter costs around $5M USD for the unit, with additional ongoing electricity costs to run the units.
Non-thermal plasma (electrically excited gas) assisted ammonia production has emerged as a pathway that doesn’t require the high operating temperature and pressure of micro-Haber Bosch systems described above.
If planned optimisation steps over the next 12 months are successful, WA startup Nitronics claims that on-farm urea production will be cost-effective against imports within 3-5 years and generate 2-5 MT urea per day with units costing less than $1M. Dr. Gunzburg says “the main thing to get away from is price volatility” and savings are particularly relevant for remote areas when considering transport costs. District level units are one opportunity, owned and managed by a co-op to supply a number of agricultural businesses.
PlasmaLeap, a start-up based in Sydney has developed an economically competitive method that uses “non-thermal plasma discharges to split air and interface nitrogen with water”.
The technology can produce green calcium nitrate or ammonium nitrate. Based upon successfully completed small-scale on-farm trials in NSW last year, full-scale trials (40ft shipping container units) will commence in Tasmania next year producing 130T N/y per unit. There is no lease or purchase cost for the unit, the producer pays for the fertiliser used. In recent discussions around potential of the technology in the livestock sector, co-founder Prof. PJ Cullen is optimistic that the solution could be cost effectively produced, powered by solar and integrated into water medicator units.
These are among the first wave of AgTech start-ups developing small scale units and this is not an exhaustive list. Most are still in active R&D and raising venture capital. Further technological advances over the next decade are certain. Yet, small-scale prototypes are even now using flexible energy sources to convert atmospheric nitrogen into agriculturally useful products on-farm.
Many research questions remain and ultimately cost effectiveness against imported fertilisers is the critical one.
Rural power supply is often supported by diesel backup generators and solar. Ease of use, reliability and access to technical support in the context of regional Australia is important. Safety and efficacy of N compounds for livestock, and quantification of potential environmental hazards through leaching and volatilisation of nitrous oxide emissions are others.
However, it is an active and exciting R&D space. Is there a future where a remote cattle property, district stock feed supplier or regional producer co-op can supply their own nitrogen needs for use in supplements, conversion into alternate proteins or support pivot irrigated and dryland crop production? If cost barriers could be overcome then small-scale, zero-emission nitrogen production units could radically alter the northern beef industry and rangeland livestock systems worldwide.
What if protein was no longer a limiting factor in our northern beef systems?
Thanks to those in the industry who have sense checked these concepts in recent days.
Lindsey Perry holds a PhD from the University of Queensland in pasture quality and emissions interactions in northern beef systems. Her experience includes roles in north Queensland NRM, QDAF and Meat & Livestock Australia’s Grassfed Beef R&D program. Her role as a beef extension officer in Cloncurry, Qld provided an ongoing respect and appreciation for the people, landscapes and challenges of northern Australia. The views expressed in this article are her own.