USING bands of light to measure hump height on cattle and ultra-violet light to sterilise knives were two efficiency improvements suggested by University of New England students at a meat processing ‘pitchfest’ today.
Other teams presented business ideas ranging from collagen-based bandages to fertiliser made from paunch contents and wastewater.
The 25 UNE students (pictured above) led by Professor in Meat Science, Peter McGilchrist, presented their business concepts during a visit to the Cannon Hill site of Australian Country Choice.
The third and fourth-year students are studying agribusiness, rural, animal or agricultural science at the Armidale-based university. They undertook a tour of the ACC facility before making their team pitchfest presentations.
ACC staff, along with AMPC’s extension and engagement manager Drew Carey and MLA’s manager, innovation development Dean Gutzke, served as judges for the bi-annual competition.
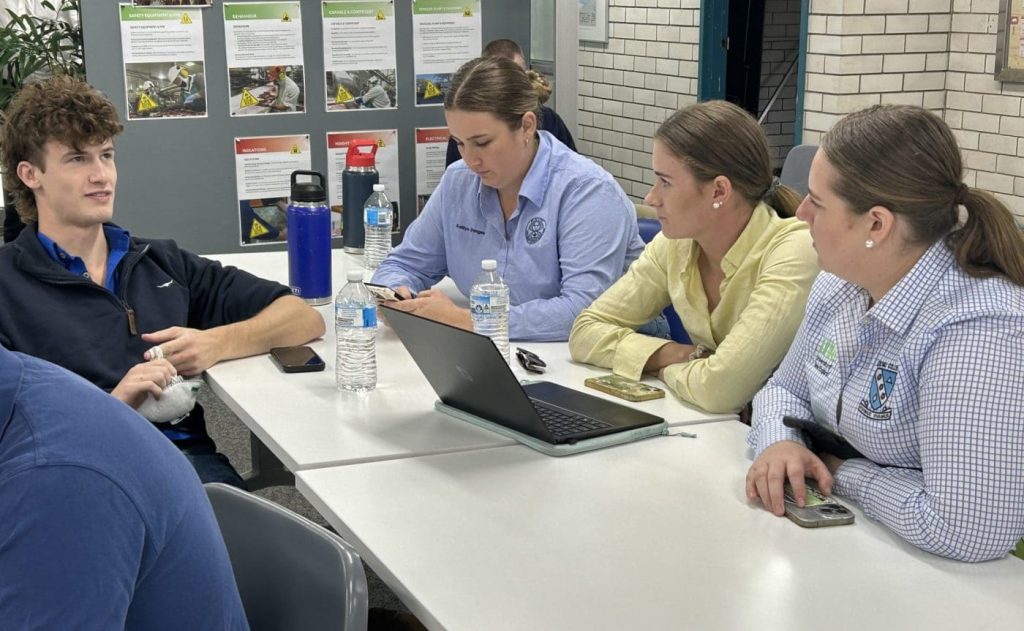
Teams prepare their pitches during the competition
Winners were the Indicus Indicator team pitching a hump height measurement system using light strips projected onto each carcase to gauge perspective. A 3D stereo camera would then measure the length from the thoracic vertebrae to the apex of the hump and the information used to estimate hump height (a proxy for indicus content).
The result would be a faster, repeatable and a more precise way to determine hump height in each carcase, replacing the current manual measurement system based on 5mm gradings.
The students argued that their automated system would reduce labour requirements at the factory but would also transfer information back to the producer and improve MSA grading. Carcases would be measured hot after the splitting saw and the data included on each carcase ticket.
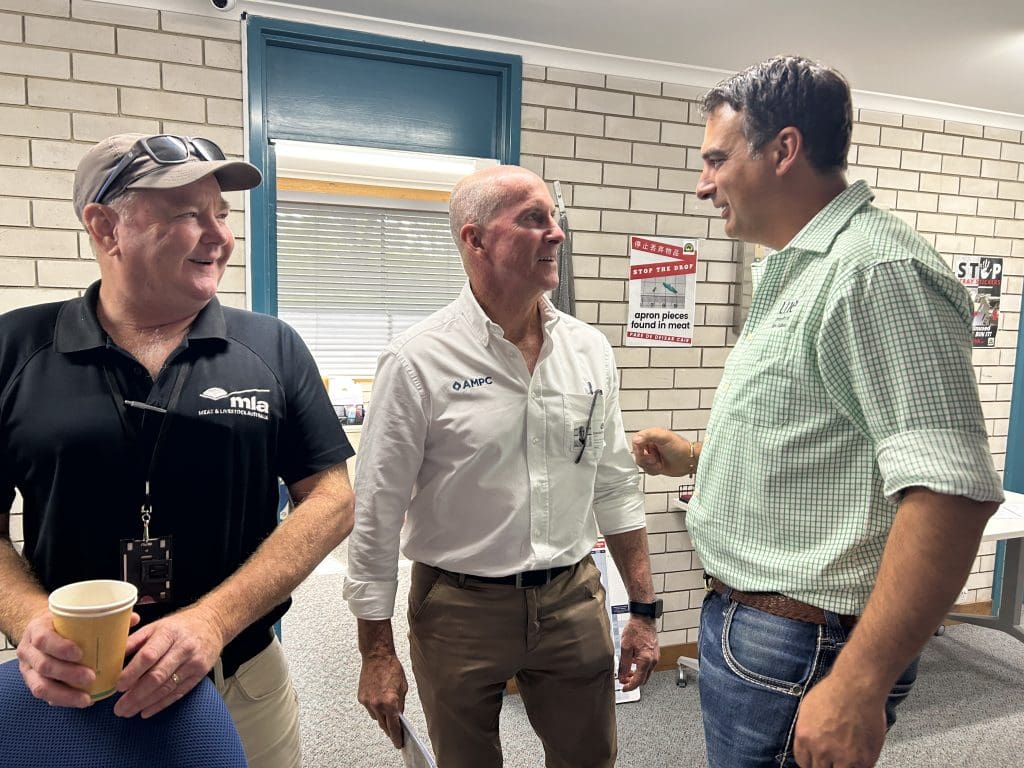
Judges confer during the Pitchfest
Light was also in the spotlight for the team pitching UV light for knife sterilisation. Their aim was to reduce water and energy use in meat processing while maintaining microbiological standards. According to their research, the students claimed current practices use four to eight litres/minute per steriliser, meaning that an abattoir operating two shifts with 40 steriliser units would use more than 280,000 litres/day.
They pitched a device costing $3000-$5000/unit fitted with a sensor that would wash and de-fat a knife with hot water jets before using UV light at 40 watts for 30 seconds to sterilise it.
The students accepted while initial costs were high, the equipment represented sizeable power and water savings over the long-term.
Paunch contents mixed with wastewater solids offered the feedstock for a composted organic fertiliser business said the team called GutGrow. Another fertiliser concept was promoted by the Skinnovate team which proposed hydrolysing low-quality hides and using enzymes to convert them into high-nitrogen sludge.
Finding new uses for hides and other sources of collagen was the inspiration of two teams; one to create specialised dressings for complicated wounds such as skin grafts and burns and the other to create a biodegradable 3D printed filament for biomedical use.
ACC’s R&D manager Paul Gibson said the bi-annual pitch-fest event with UNE final year students and staff provided exposure to commercial opportunities for careers in the red meat industry.
“The event is focussed on identifying new opportunities in factory sustainability for water, waste and energy management,” he said.
HAVE YOUR SAY